Gauges are versatile tools used in various industries to measure and verify the thickness, pressure, or dimensions of different materials and systems. These instruments play a crucial role in ensuring accuracy, quality control, and safety in manufacturing processes.
One common type of gauge is the plain type gauge. This gauge is used to measure the thickness of materials such as metal sheets, plastic films, or paper. It consists of a flat, non-adjustable surface that is placed against the material to determine its thickness.
Another type of gauge is the snap gauge or gap gauge. This gauge is designed to measure the gap between two surfaces or the outer diameter of cylindrical objects. It typically consists of two or more movable arms or jaws that are adjusted to fit the desired measurement.
Ring type gauges, on the other hand, are used to measure the inner or outer diameter of cylindrical objects. These gauges come in various sizes and shapes to accommodate different objects, such as pipes, shafts, or bearings.
Limit type gauges are used to determine if a part or component falls within acceptable tolerances. These gauges have specific upper and lower limits, and the part being measured must fit within these limits to be considered acceptable.
Pin type gauges are used to measure the size or depth of holes or slots. These gauges consist of a cylindrical pin with a calibrated scale, allowing for precise measurements.
Caliper type gauges, also known as vernier calipers, are versatile tools used to measure dimensions such as length, width, or thickness. They consist of two jaws that can be adjusted to fit the object being measured, providing accurate readings.
Feeler type gauges are thin strips of metal used to measure small gaps or clearances. They are often used in automotive and engineering industries to check the clearance between components or to set the proper gap in spark plugs or valves.
Screw pitch gauges are specialized tools used to measure the pitch or thread spacing of screws or bolts. They consist of a set of blades with different thread profiles, allowing for quick identification and measurement of screw threads.
In addition to these specific types, there are also general-purpose gauges such as dial or digital gauges that can be used for various measuring purposes. These gauges often provide precise and easy-to-read measurements, making them popular choices in many industries.
Gauges are essential tools used in a wide range of industries to ensure accuracy, quality control, and safety. From measuring thickness and dimensions to monitoring pressure, these instruments play a vital role in maintaining the standards and regulations of different materials and systems.
What Are The Types Of Gauge?
There are several types of gauges used for various measuring purposes. Here is a detailed list of the different types of gauges:
1. Plain Type Gauge: This is a basic type of gauge used to measure the dimensions of objects. It consists of a flat plate with markings or a scale to indicate the measurements.
2. Snap Gauges or Gap Gauges: These gauges are used to measure the gap or distance between two surfaces. They typically consist of two jaws or plates that can be adjusted to fit different sizes.
3. Ring Type Gauge: This type of gauge is used to measure the diameter of cylindrical objects. It consists of a circular ring with a calibrated scale or markings.
4. Limit Type Gauge: A limit gauge is used to check whether a certain dimension of an object falls within acceptable limits. It typically consists of go and no-go gauges, where the go gauge checks for conformity and the no-go gauge checks for non-conformity.
5. Pin Type Gauge: This gauge is used to measure the diameter or thickness of small holes or slots. It consists of a cylindrical pin with calibrated markings.
6. Caliper Type Gauge: A caliper gauge is used to measure the distance between two points or the dimensions of an object. It consists of two jaws or arms that can be adjusted to fit different sizes.
7. Feeler Type Gauge: This is a thin strip or wire used to measure small gaps or clearances between components. It is commonly used in automotive and engineering applications.
8. Screw Pitch Gauges: These gauges are used to measure the pitch or thread spacing of screws, bolts, or nuts. They consist of a set of blades with calibrated markings.
These are some of the main types of gauges used in various industries for measuring dimensions, distances, clearances, and other parameters. Each type of gauge has its own specific application and is designed to provide accurate measurements in its respective field.
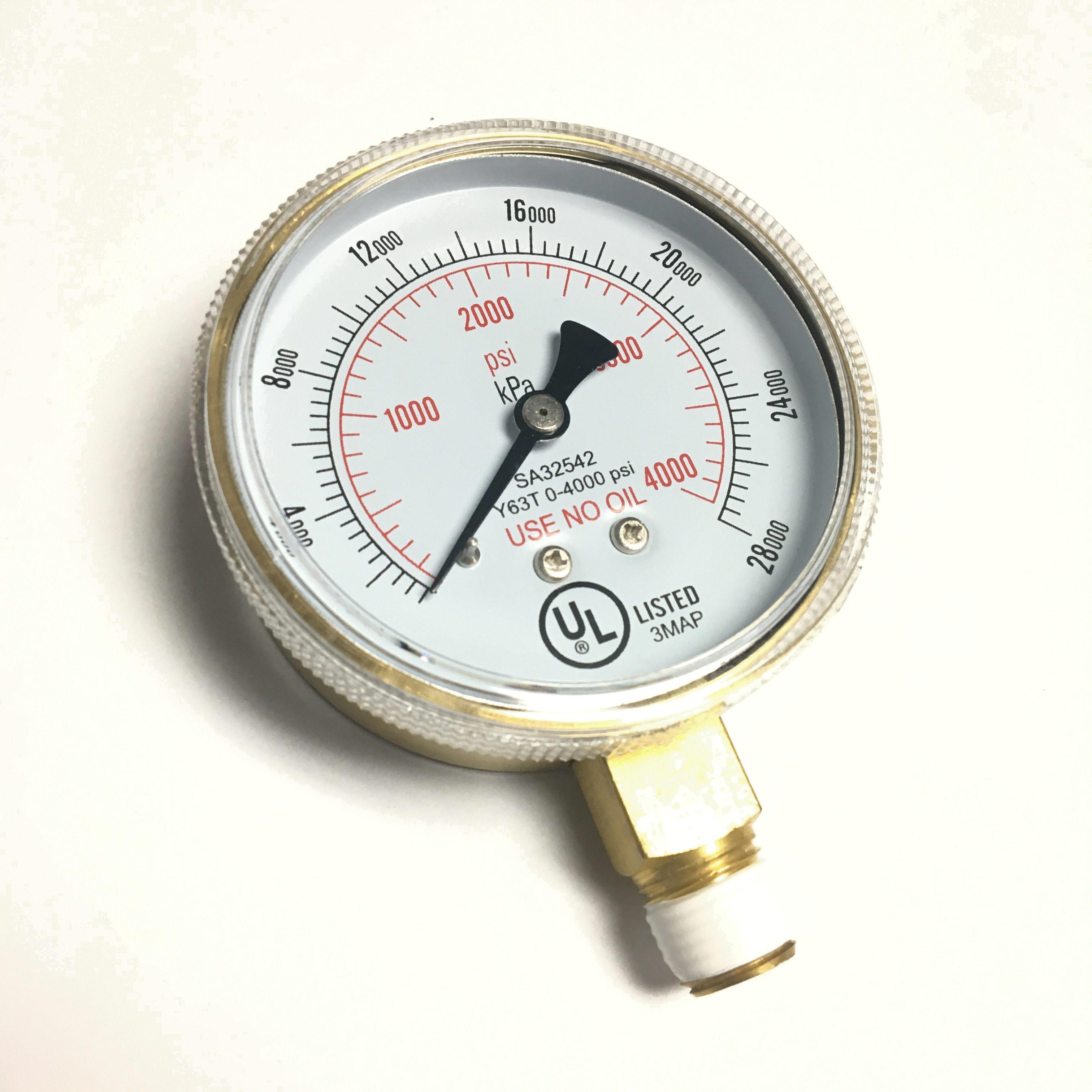
What Is Gauge A Measure Of?
Gauge is a measure of thickness. It is used to quantify the thickness or diameter of various materials, such as wires, sheets, and pipes. The term “gauge” originated in the British iron wire industry during a time when there was no universal unit of thickness. The sizes of the gauge numbers were determined by the process of wire-drawing and the properties of iron as a substance. Here are some key points about the concept of gauge as a measure of thickness:
1. Gauge measures thickness: Gauge is primarily used to measure the thickness of materials. It provides a standardized way to express the thickness or diameter of various objects.
2. Origin in the iron wire industry: The concept of gauge originated in the British iron wire industry. In the early days, wire was drawn through dies to reduce its diameter. The process of wire-drawing resulted in wires of different thicknesses, which were assigned gauge numbers to represent their sizes.
3. No universal unit of thickness: Before the introduction of gauge numbers, there was no universal unit of thickness. Different industries and regions used their own measurement systems, leading to confusion and inconsistency. Gauge numbers helped to establish a common standard for expressing thickness.
4. Wire-drawing process: The gauge numbers were determined by the wire-drawing process itself. As wire was drawn through progressively smaller dies, its diameter decreased. The gauge numbers were assigned based on the number of times the wire was passed through the dies.
5. Nature of iron as a substance: Iron, being a malleable material, allowed for the wire-drawing process to produce wires of varying thicknesses. The properties of iron played a role in determining the range of gauge numbers and their corresponding thicknesses.
To summarize, gauge is a measure of thickness that originated in the British iron wire industry. It provided a standardized way to express the thickness or diameter of various materials. The gauge numbers were determined by the wire-drawing process and the properties of iron as a substance.
What Are Thickness Gauges Used For?
Thickness gauges are utilized in various industries, primarily in engineering and manufacturing, to accurately measure the thickness of materials. These devices play a crucial role in ensuring that the thickness of materials adheres to industrial standards and regulations. By measuring the thickness, thickness gauges assist in quality control and help identify any deviations or inconsistencies in the material thickness.
The primary purpose of thickness gauges is to provide quick and easy measurements of material thickness. They are commonly used in industries such as metalworking, automotive manufacturing, construction, and aerospace, among others. These gauges allow engineers and manufacturers to verify that the materials being used meet the required thickness specifications.
Some specific applications of thickness gauges include:
1. Quality Control: Thickness gauges help in maintaining consistent quality by ensuring that materials meet the specified thickness requirements. This is particularly important in industries where precision and accuracy are critical.
2. Compliance with Standards: Many industries have specific standards and regulations regarding material thickness. Thickness gauges help to ensure that materials comply with these standards, reducing the risk of non-compliance and potential legal issues.
3. Preventing Defects: Thickness variations in materials can lead to defects or structural weaknesses. By accurately measuring thickness, these gauges help identify any potential defects early on, allowing for necessary adjustments or repairs.
4. Material Selection: Thickness gauges assist in selecting the appropriate materials for specific applications. By measuring thickness, engineers can determine whether a material is suitable for a particular purpose or if an alternative material should be considered.
5. Cost Optimization: In industries where materials are a significant cost factor, thickness gauges help optimize material usage. By ensuring that materials are used efficiently and within the required thickness range, unnecessary waste and costs can be minimized.
Thickness gauges are indispensable tools in engineering and manufacturing industries. They enable precise measurement of material thickness, ensuring compliance with standards, preventing defects, and optimizing cost and material usage.
Why Do We Use Pressure Gauges?
Pressure gauges are utilized in various industries for a multitude of reasons. Here are the key purposes for using pressure gauges:
1. Quality Control: Pressure gauges are essential instruments in ensuring the quality of products. By monitoring the pressure within a system, they help maintain consistency and accuracy in manufacturing processes. This is particularly crucial in industries such as pharmaceuticals, food processing, and automotive, where precise pressure control is necessary.
2. Safety Assurance: One of the primary functions of pressure gauges is to ensure the safety of both personnel and equipment. By monitoring the pressure in fluids, gases, and steam, pressure gauges can detect leaks, abnormal pressure build-up, or any other potential hazards. This helps prevent accidents, damage to equipment, and the release of dangerous substances.
3. System Performance Evaluation: Pressure gauges provide valuable information about the performance of a system. By monitoring pressure levels, operators can assess the efficiency and effectiveness of equipment, identify any abnormalities, and make necessary adjustments or repairs. This helps optimize system performance, reduce downtime, and improve overall productivity.
4. Process Monitoring and Control: In many industrial processes, maintaining precise pressure levels is critical. Pressure gauges enable operators to monitor pressure variations in real time and make necessary adjustments to ensure optimal process conditions. This is particularly important in industries such as chemical manufacturing, oil and gas, and power generation, where slight pressure changes can significantly impact the outcome of the process.
5. Compliance with Standards and Regulations: Pressure gauges play a vital role in meeting industry standards and regulatory requirements. Many industries have specific guidelines regarding pressure limits and monitoring. By using pressure gauges, companies can demonstrate compliance with these standards, ensuring the safety and quality of their products.
6. Troubleshooting: When issues arise in a system, pressure gauges can be valuable diagnostic tools. By analyzing pressure fluctuations or abnormalities, operators can identify potential problems, such as clogged filters, faulty valves, or blocked pipes. This allows for prompt troubleshooting and prevents further damage or system failures.
Pressure gauges are indispensable tools in various industries, serving purposes such as quality control, safety assurance, system performance evaluation, process monitoring and control, compliance with standards, and troubleshooting. By providing accurate and real-time pressure readings, they contribute to the smooth operation, efficiency, and safety of industrial processes.
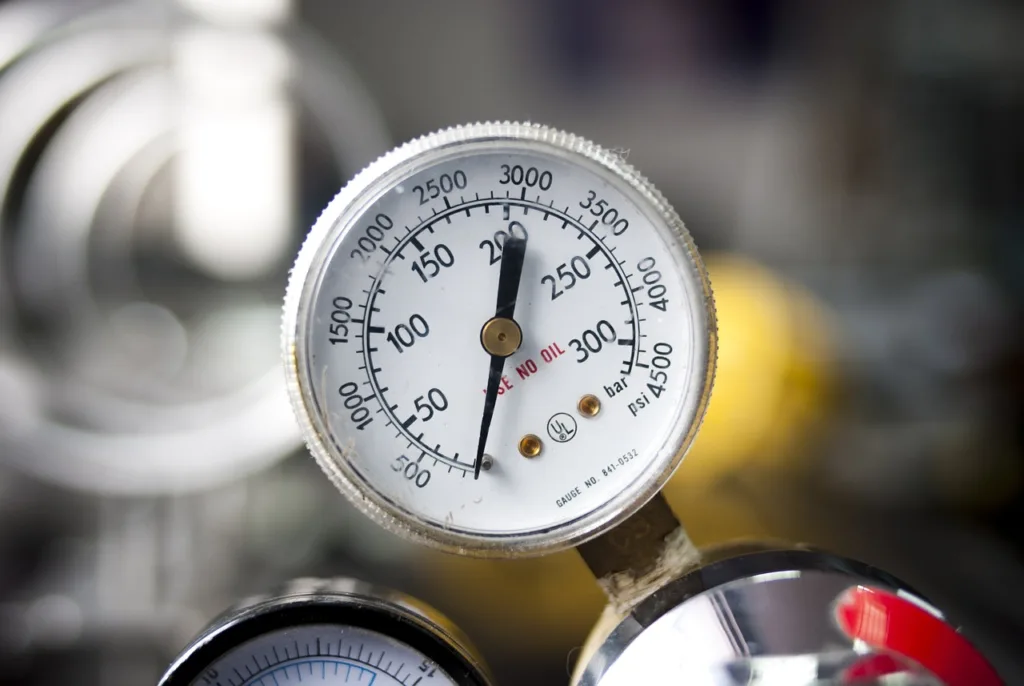
Conclusion
Gauges are crucial tools used in various industries to measure and monitor thickness and pressure. They come in different types, such as plain, snap, ring, limit, pin, caliper, feeler, and screw pitch gauges, each serving a specific purpose.
Plain type gauges are commonly used to measure the thickness of materials, while snap gauges or gap gauges are designed to quickly check if a part or component fits within specified tolerances. Ring type gauges are used to measure the external diameter of cylindrical objects, and limit type gauges are used to ensure that a part’s dimensions fall within acceptable limits.
Pin type gauges are used to measure the internal diameter of holes or bores, while caliper type gauges are versatile tools that can measure both inside and outside dimensions. Feeler type gauges, on the other hand, are used to measure small gaps or clearances, and screw pitch gauges are specifically designed to measure the pitch or distance between screw threads.
Gauges play a critical role in ensuring quality control and compliance with industry standards. They help manufacturers and engineers maintain consistency in material thickness, monitor pressure levels, and ensure the proper functioning of systems and components. With the wide range of gauge types available, industries can choose the most suitable gauge for their specific needs, making them an essential tool in various sectors.