In the world of Engineering and Manufacturing, there are key terms that are used to define the accuracy of a product. Two of these terms are True Position and Position. While they may seem similar, they have distinct differences that are important to understand.
Position is a term used to define the location of a feature on a part or product. This location is defined by its X, Y, and Z coordinates. Position is often toleranced in engineering drawings to ensure that the feature is located within a specified range of its nominal location.
True Position is a more stringent requirement than Position. It defines the location of a feature in relation to a set of datums, which are reference points or planes on the part or product. True Position takes into account not only the X, Y, and Z coordinates of the feature but also its orientation and size. It is calculated as twice the 3D distance between the measured and the nominal point.
True Position is an important requirement in engineering and manufacturing becase it ensures that parts fit and function as intended. It is especially important in applications where parts must be interchangeable or when a part must fit into a larger assembly. For example, in the aerospace industry, true position tolerances are often used to ensure that critical components such as engine mounts and landing gear are located correctly.
Measuring true position requires precise equipment and careful measurement techniques. One common method is to use a coordinate measuring machine (CMM), which uses a probe to measure the X, Y, and Z coordinates of a feature in relation to the datums. Another method is to use a gauge that has been calibrated to the required tolerance.
While position and true position may seem similar, they have distinct differences that are important to understand in engineering and manufacturing. True Position is a more stringent requirement that takes into account not only the location of a feature but also its orientation and size in relation to a set of datums. Measuring true position requires precise equipment and careful measurement techniques to ensure the accuracy of the part or product.
What Does True Position Mean?
True position is a term used in Geometric Dimensioning and Tolerancing to refer to the exact coordinate or location of a feature defined by basic dimensions or other means that represents its nominal value. It is the ideal location where the feature is intended to be placed. The true position is determined by the designer or engineer, and it serves as the reference point for the manufacturing process. The position tolerance, on the other hand, refers to the allowable variation from the true position that is stll acceptable. In other words, it is the maximum deviation that is allowed from the intended location of the feature. The position tolerance is specified in the engineering drawing and is used by the manufacturer to ensure that the feature is produced within the acceptable limits. The true position and position tolerance are critical aspects of engineering design and manufacturing, as they ensure that the final product meets the required specifications and functions as intended.
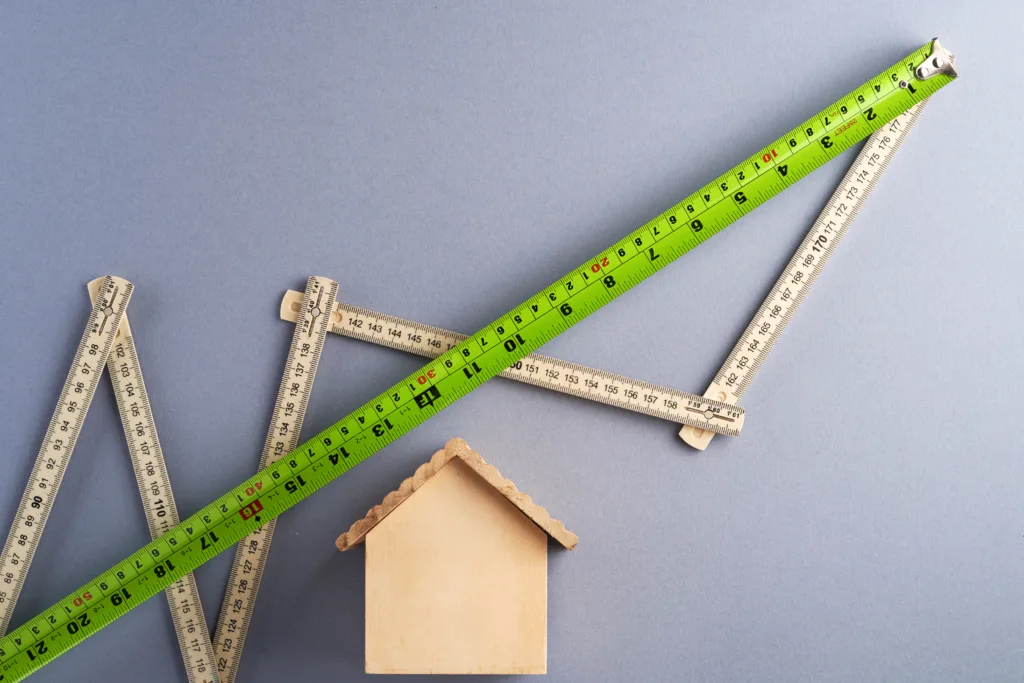
How Do You Calculate True Position?
True position is calculated by taking the 3D distance between the measured point and the nominal point, and then multiplying this value by 2. This results in a number that represents the diameter of a sphere around the nominal point, which contains the actual point. This calculation is used to determine the accuracy of a feature’s location in relation to its intended position. The true position value is an important metric in engineering and manufacturing, as it helps to ensure that parts and components are manufactured and assembled correctly.
Does True Position Need A Datum?
True Position requires a Datum. In Geometric Dimensioning and Tolerancing (GD&T), True Position is a measurement of the exact location of a feature in relation to a reference point or points called Datums. These Datums serve as a reference for the coordinate system used to measure the True Position. The Feature Control Block (FCB) used to specify True Position always includes a Datum reference, which is usually identified by a letter (e.g. A, B, C). Without a Datum reference, it would be impossible to accurately determine the True Position of a feature, as it would have no point of reference. Therefore, in order to properly apply GD&T and measure True Position, a Datum reference is necessary.
What Is True Position In CMM?
True position in Coordinate Measuring Machine (CMM) is a measurement of the accuracy of the position of a feature or part in relation to the datum or reference plane. It is a fundamental geometric dimension used to ensure that the location of a feature or part is within the specified tolerance range.
The true position is determined by measuring the distance between the actual position of the feature or part and the theoretical position specified by the designer. The measurement is typically performed using a probe that touches the surface of the part and records its position in three-dimensional space.
The true position is expressed using a set of coordinates that describe the distance and direction of the feature or part from the datum. The tolerance for the true position is specified in the design drawing and is typically expressed in terms of a distance or a percentage of the oerall dimension.
True position in CMM is a critical measurement used to ensure that the location of a feature or part is within the specified tolerance range. It is determined by measuring the distance between the actual position of the feature or part and the theoretical position specified by the designer, using a probe that records its position in three-dimensional space.
Conclusion
Understanding the difference between true position and position is crucial when it comes to precision engineering and manufacturing. While position refers to the nominal value or desired location of a feature, true position represents the actual location of the feature relative to the datum. The true position tolerance specifies how much variation is allowed from the nominal position, and is calculated as twice the 3D distance between the measured and nominal points. By identifying the correct datums in the feature control block, manufacturers can ensure that their products are produced to the required level of accuracy and meet customer expectations. Whether usng gauges or coordinate measuring machines, measuring true position is essential for ensuring the quality and precision of products in a variety of industries.