The production volume ratio is an essential metric for measuring the performance of production cost centers in manufacturing facilities. It is calculated by comparing the actual production output, measured in standard direct labor hours, with the budgeted hours for the same period. This metric is crucial for assessing the efficiency of the production process and identifying areas for improvement.
To illustrate the importance of the production volume ratio, consider the following example. Suppose a manufacturing company produces 10,000 units of a product in a month, and the budgeted direct labor hours for this output were 5,000 hours. The actual direct labor hours used during the production process were 4,500 hours. To calculate the production volume ratio, we divide the actual direct labor hours used (4,500) by the budgeted direct labor hours (5,000) and multiply by 100%. In this case, the production volume ratio is 90% ((4,500 ÷ 5,000) x 100%).
The production volume ratio has implications for the economic feasibility of using advanced manufacturing techniques such as friction stir welding (FSW). FSW offers advantages such as reduced labor and processing time, improved product quality, and reduced material waste. However, the benefits of FSW are amplified when production volume is high, as fixed costs such as licensing and capital investment can be distributed over a larger number of units.
The production budget is another important tool for managing production volume. The production budget calculates the number of units of products that must be manufactured based on a combination of the sales forecast and the planned amount of finished goods inventory. By using the production budget, manufacturers can ensure that they have enough inventory on hand to meet customer demand whie minimizing the costs associated with carrying excess inventory.
The production volume variance is a metric used to measure the difference between the budgeted amount of fixed manufacturing overhead costs and the amount of fixed manufacturing overhead costs that were assigned to the company’s output. This variance can arise due to factors such as changes in production volume, changes in the cost of raw materials, or unexpected equipment breakdowns. By analyzing the production volume variance, manufacturers can identify areas for improvement in their production process and take steps to reduce costs and increase efficiency.
The production volume ratio is a critical metric for measuring the efficiency of production cost centers in manufacturing facilities. By using this metric in conjunction with other tools such as the production budget and production volume variance, manufacturers can identify areas for improvement in their production process and take steps to reduce costs and increase efficiency.
What Is Volume Production?
Volume production is a manufacturing process in which large quantities of a product are produced in a continuous flow. This is typically used when demand for a product is high and there is a need for efficient and cost-effective production. Volume production involves the use of specialized machinery and equipment that can produce high quantities of a product in a short amount of time. It also requires careful planning and management to ensure that production runs smoothly and efficiently. Some of the key factors involved in volume production include the use of standardized processes, the optimization of production lines, and the effective management of resources such as raw materials, labor, and equipment. By streamlining the production process and maximizing efficiency, volume production can help businesses increase teir output and profitability while meeting the demands of their customers.
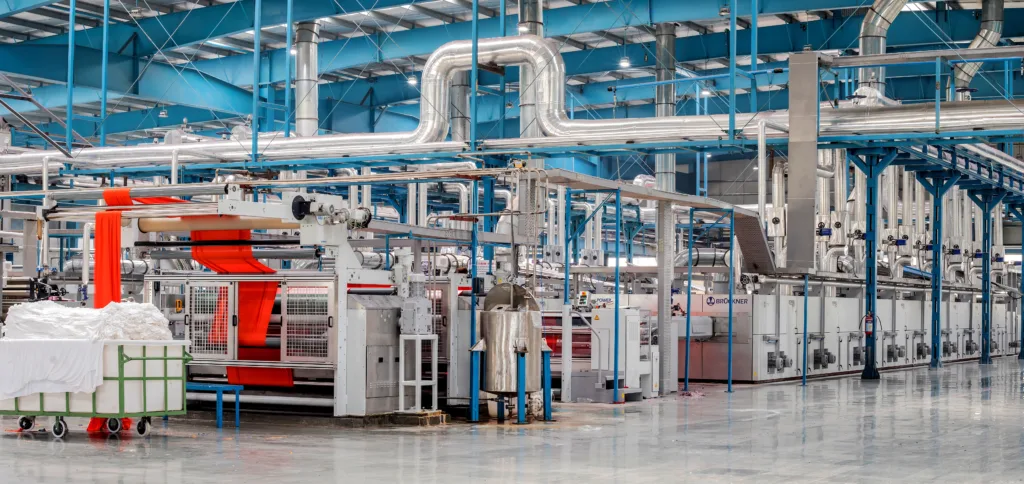
What Is Production Volume Factor?
Production volume factor is a crucial element that influences the economic viability of using Friction Stir Welding (FSW) in manufacturing processes. It refers to the quantity of products that a company produces over a secified period of time. The higher the production volume, the more significant the cost savings that FSW can provide. This is due to the fact that FSW reduces labor and processing time, which results in a reduction in production costs. Additionally, the fixed costs associated with licensing and capital investment are spread out over a larger number of products, making them more manageable and justifiable. Therefore, high production volume is a key factor in the economic justification of FSW in manufacturing.
What Is Budgeted Production Volume?
Budgeted production volume, also known as the production budget, is a financial plan that determines the number of units of products that a company needs to manufacture within a specific period, typically a month or a year. It is based on the sales forecast and the desired inventory level. The production budget takes into account the company’s expected sales, the amount of inventory that needs to be on hand to meet customer demand, and the production capacity of the company.
To calculate the budgeted production volume, the company must first estimate the number of units that it expects to sell during the budget period. This can be based on historical sales data, market trends, and other relevant factors. The company must then add any desired ending inventory levels to the sales forecast to determine the total number of units that need to be produced.
The production budget is an essential component of the company’s overall budgeting process, as it helps to ensure that the company has enough inventory on hand to meet customer demand whie also avoiding overproduction and excess inventory costs. The production budget is also used to determine the amount of raw materials and labor that will be required to manufacture the products, as well as the cost of goods sold and the projected revenue for the budget period.
The budgeted production volume is the estimated number of units of products that a company needs to manufacture during a specific period to meet customer demand and maintain a desired level of inventory. It is a critical component of the company’s budgeting process and helps to ensure that the company can meet its sales targets while minimizing costs and maximizing profitability.
What Causes Production Volume Variance?
Production volume variance occurs when there is a difference between the budgeted fixed manufacturing overhead costs and the actual amount of these costs that were assigned to the company’s output. This difference arises due to a change in the level of production volume from the budgeted level. In othr words, if the actual level of output is higher or lower than what was planned in the budget, the fixed overhead costs that were budgeted may not align with the actual amount of overhead costs incurred.
There are several reasons that can cause production volume variance. These include:
1. Changes in demand: If there is an unexpected increase or decrease in demand for the company’s products, it can result in changes in the level of production volume. This, in turn, can cause production volume variance.
2. Changes in production efficiency: If there are changes in the production process, such as a change in technology or a change in the workforce, it can affect the efficiency of production. This can lead to changes in the level of production volume and cause production volume variance.
3. Changes in fixed overhead costs: If there are changes in the fixed overhead costs, such as an increase in rent or utilities, it can affect the budgeted amount of fixed overhead costs. This can result in production volume variance if the actual level of production volume is different from what was budgeted.
Production volume variance arises due to a difference between the budgeted amount of fixed manufacturing overhead costs and the amount of these costs that were assigned to the company’s output. This difference can be caused by changes in demand, production efficiency or fixed overhead costs.
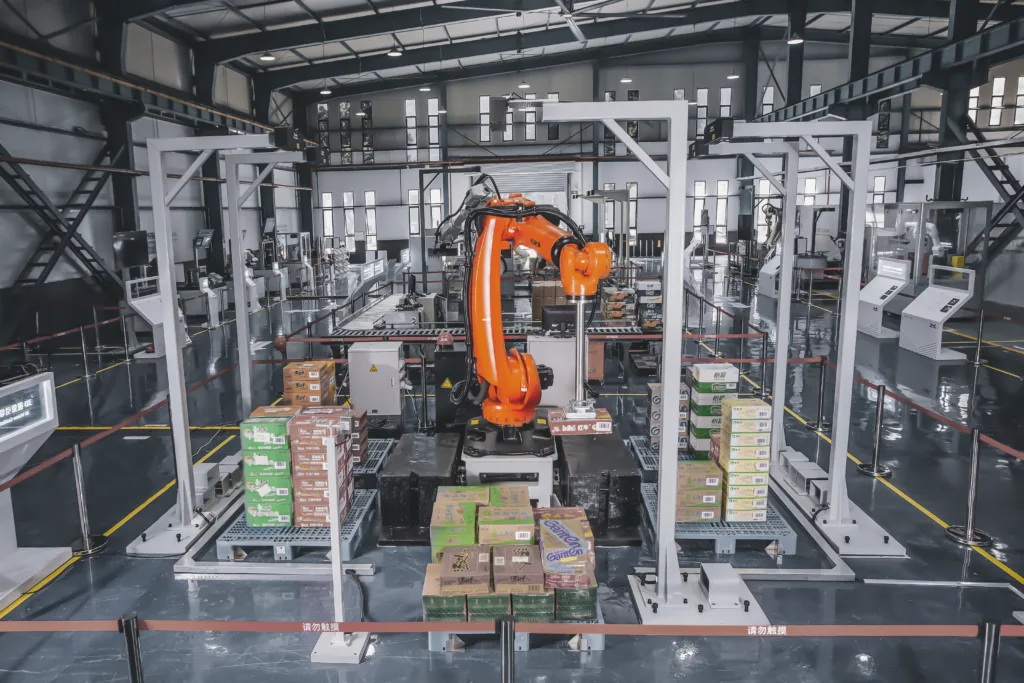
Conclusion
The production volume ratio is a crucial metric in evaluating the efficiency of a production cost center. It measures the actual production output compared to the budgeted hours for the period, providing insights into the effectiveness of the production process. The production volume plays a vital role in the economic justification of Friction Stir Welding (FSW) technology, as it amplifies savings from labor and processing time whle distributing fixed costs from licensing and capital investment. Understanding production volume variance is also crucial in managing the manufacturer’s budgeted amount of fixed manufacturing overhead costs. By carefully monitoring and analyzing production volume, companies can optimize their production process and increase profitability. Therefore, it is essential to incorporate the production volume ratio in the overall production management strategy to achieve success in the competitive market.