Flow separation is a phenomenon in aerodynamics that can have significant negative effects on the performance of an aircraft or any object moving through a fluid medium. When flow separation occurs, the smooth flow of air or gas around the object is disrupted, causing a loss of lift and an increase in pressure drag.
One of the main reasons why flow separation is considered bad is because it leads to a reduction in lift. Lift is the force that allows an aircraft to stay airborne, and any decrease in lift can have serious consequences. When flow separation occurs, the airflow over the top surface of the object, such as an airplane wing, becomes detached from the surface. This results in a decrease in the suction or negative pressure that helps generate lift. As a result, the object experiences a loss of lift, making it more difficult to maintain altitude or even causing it to descend.
In addition to the loss of lift, flow separation also leads to an increase in pressure drag. Pressure drag is a form of drag that is caused by the difference in pressure between the front and rear surfaces of the object. When flow separation occurs, this pressure differential becomes more pronounced, leading to increased drag. This can have a detrimental effect on the overall performance of the object, as it requires more energy or power to overcome the increased drag and maintain a desired speed or efficiency.
Flow separation is typically caused by factors such as an excessive angle of attack, rough or uneven surfaces, or inadequate design of the object. When the angle of attack, which is the angle between the object’s surface and the direction of the oncoming flow, becomes too high, the flow of air or gas can no longer follow the contours of the object smoothly. This leads to the separation of the flow from the surface, resulting in flow separation.
Rough or uneven surfaces can also disrupt the flow of air or gas and contribute to flow separation. Any imperfections or irregularities on the surface of the object can create disturbances in the flow, causing it to separate and form turbulent vortices downstream of the separation point. These vortices further disrupt the flow, increasing drag and reducing the overall efficiency of the object.
Inadequate design of the object, such as poorly shaped wings or body, can also contribute to flow separation. The shape of an object plays a crucial role in determining how the flow of air or gas interacts with its surface. If the design is not optimized for smooth airflow, flow separation is more likely to occur.
Flow separation is considered bad because it leads to a decrease in lift and an increase in pressure drag. These effects can have significant consequences for the performance and efficiency of an object moving through a fluid medium, such as an aircraft. Understanding the causes and consequences of flow separation is crucial in the design and operation of aerodynamic systems to minimize its negative effects and improve overall performance.
What Are The Two Major Consequences Of Flow Separation?
Flow separation in aerodynamics can lead to two significant consequences: reduced lift and increased pressure drag. Let’s explore each consequence in detail:
1. Reduced Lift:
Flow separation occurs when the airflow over an object, such as an aircraft wing, fails to follow the desired smooth path. Instead, the flow detaches or separates from the surface, creating a region of low pressure behind the object. This separation disrupts the generation of lift, which is the force that opposes gravity and allows an aircraft to stay airborne.
When flow separation occurs, the separation bubble creates a larger pressure difference between the upper and lower surfaces of the object. This pressure difference diminishes the lift generated by the wing, reducing its overall efficiency. As a result, the aircraft may experience a decrease in lift, potentially leading to decreased stability and maneuverability.
2. Increased Pressure Drag:
Flow separation also leads to an increase in pressure drag. Pressure drag is the resistance or force experienced by an object as a result of the pressure differential between the front and rear surfaces. When the flow separates, the low-pressure area behind the object creates a suction effect, pulling the object backward.
This suction effect increases the pressure drag, which is the component of drag that is caused by the difference in pressure on the object’s surfaces. Pressure drag is undesirable as it requires additional energy to overcome, reducing the overall efficiency and performance of the object, such as an aircraft or a vehicle.
The two major consequences of flow separation in aerodynamics are reduced lift and increased pressure drag. Flow separation disrupts the smooth flow of air over an object, leading to a decrease in lift and an increase in pressure drag. These consequences can have significant implications for the efficiency, stability, and maneuverability of aircraft and other objects that rely on aerodynamic principles.
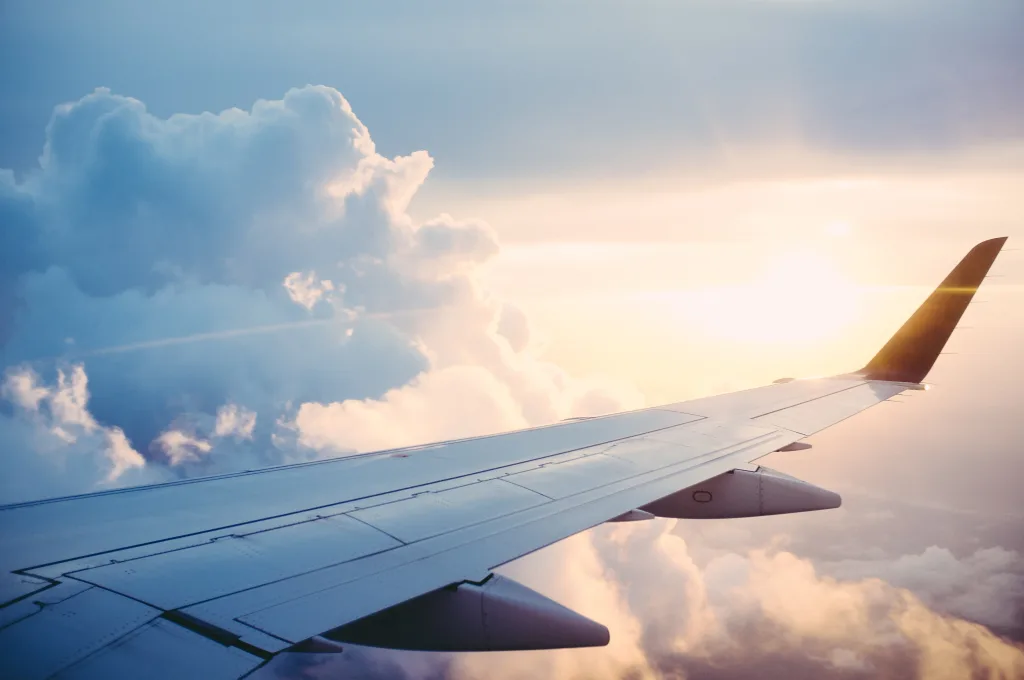
Why Does Flow Separation Cause Loss Of Lift?
Flow separation occurs when the airflow over an airfoil becomes disrupted, leading to a loss of lift. This phenomenon is typically caused by an increase in the angle of attack or a change in the airfoil’s shape.
When the angle of attack is too high, the airflow on the upper surface of the airfoil becomes turbulent. This turbulence disrupts the smooth flow of air, causing it to separate from the surface of the airfoil. As a result, the suction or low-pressure area on the top surface of the airfoil decreases, leading to a reduction in lift.
Similarly, changes in the airfoil’s shape can also lead to flow separation. If the airfoil is altered in a way that it deviates from its optimal design, the airflow may not be able to follow the desired path smoothly. As a result, separation occurs, and the lift generated by the airfoil decreases.
The loss of lift due to flow separation can be explained in the following points:
1. Reduction in effective angle of attack: Flow separation causes a reduction in the effective angle of attack of the airfoil. The angle of attack is the angle between the chord line of the airfoil and the oncoming airflow. When flow separation occurs, the effective angle of attack becomes smaller than the actual angle of attack. This reduction in the effective angle of attack leads to a decrease in the lift generated by the airfoil.
2. Decreased suction on the top surface: Flow separation disrupts the smooth flow of air over the top surface of the airfoil. As a result, the low-pressure or suction area on the top surface decreases. This reduction in suction reduces the pressure difference between the top and bottom surfaces of the airfoil, thereby reducing the lift generated.
3. Lower pressure on the bottom surface: In addition to the reduced suction on the top surface, flow separation also affects the pressure on the bottom surface of the airfoil. As the airflow separates from the airfoil, the pressure on the bottom surface increases. This increased pressure counteracts the lift generated by the airfoil, further contributing to the loss of lift.
4. Flattening of the lift curve slope: Flow separation alters the lift characteristics of the airfoil. As separation starts to occur, the lift curve slope becomes flatter, indicating a decrease in lift generation. In extreme cases, the lift curve slope may even reverse, indicating a full stall where lift is completely lost.
Flow separation disrupts the smooth flow of air over an airfoil, leading to a decrease in lift. This is primarily caused by a reduction in the effective angle of attack, decreased suction on the top surface, increased pressure on the bottom surface, and a change in the lift curve slope.
What Happens When Flow Separates?
When flow separates, it means that the flow of either a liquid or gas around a particular object or body deviates from its surface and creates an area of reversed or backward vortex flow. This separation of flow typically occurs when the fluid encounters a sharp change in direction or encounters an obstruction.
Here is a more detailed explanation of what happens when flow separates:
1. Reverse-Vortex Flow Area: When flow separation occurs, it leads to the formation of a reverse-vortex flow area. This area is characterized by the fluid moving in a direction opposite to the main flow, creating a swirling or rotating motion in the opposite direction.
2. Pressure Gradients: Flow separation is accompanied by the presence of small pressure gradients in the reverse-vortex flow area. These pressure gradients are a result of the fluid’s change in direction and the formation of the swirling motion. The pressure in this area is typically lower than in the main flow region.
3. Stagnation Pressure Reduction: Another consequence of flow separation is a reduction in stagnation pressure. Stagnation pressure refers to the pressure of the fluid when it is brought to rest or stagnation. In the reverse-vortex flow area, the fluid experiences reduced stagnation pressure due to the swirling motion and the presence of lower pressures.
4. Turbulence and Mixing: Flow separation often leads to the generation of turbulence in the reverse-vortex flow area. The swirling motion of the fluid causes mixing of different fluid layers, resulting in increased turbulence levels. This turbulence can have various effects depending on the specific application, such as increased heat transfer or increased drag on a body.
When flow separates, it creates a reverse-vortex flow area characterized by small pressure gradients and reduced stagnation pressure values. This separation of flow is typically caused by sharp changes in direction or obstructions encountered by the fluid. The resulting reverse-vortex flow area exhibits swirling motion, reduced pressures, and increased turbulence.
Does Flow Separation Cause Turbulence?
Flow separation can indeed cause turbulence. When the boundary layer detaches itself from the surface of an object, such as an aircraft wing or a car body, it creates a region of flow separation. This separation point is where the flow begins to separate from the surface and move in a different direction.
As the flow separates, vortices often form downstream of the separation point. These vortices are regions of swirling flow, and they can lead to a turbulent flow regime. Turbulence refers to irregular and chaotic flow patterns characterized by fluctuations in velocity, pressure, and other flow properties.
The vortices formed due to flow separation can cause the flow to become more turbulent. Turbulent flows are characterized by the presence of eddies and fluctuations in flow properties, which can result in increased drag, reduced lift, and other undesirable effects.
Flow separation can lead to the formation of vortices and the onset of turbulence. This turbulent flow can have significant impacts on the performance and behavior of objects in fluid flow, such as aircraft, vehicles, and other structures.
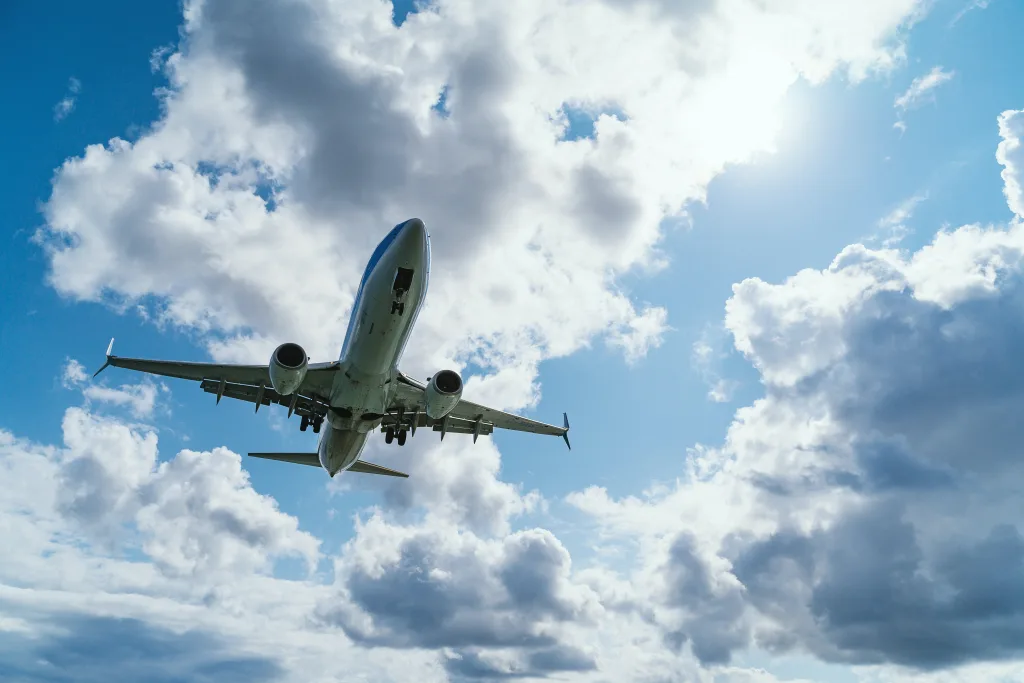
Conclusion
Flow separation is a phenomenon in aerodynamics where the flow around an object detaches from its surface, resulting in reduced lift and increased pressure drag. This occurs due to the pressure differential between the front and rear surfaces of the object. The altered shape of the airfoil leads to a decrease in the effective angle of attack, causing a decrease in both the suction on top and the pressure on the bottom of the object. As a result, there is a loss of lift and a flattening of the lift curve slope, which can eventually lead to a full stall.
Flow separation is characterized by the formation of a reverse-vortex flow area, which is accompanied by small pressure gradients and reduced stagnation pressure values. The boundary layer or flow begins to detach itself from the body surface, leading to a boundary layer separation or flow separation. Downstream of the separation point, vortices often form, resulting in a turbulent flow.
Understanding flow separation is crucial in aerodynamics, as it has significant implications for the performance and stability of aircraft and other objects moving through a fluid medium. By studying and analyzing flow separation, engineers and designers can develop strategies to minimize its occurrence and mitigate its negative effects on lift and drag. This knowledge is essential for optimizing the efficiency, maneuverability, and safety of various aerodynamic systems.